When you install a DC Disconnect switch and operate it for maintenance purposes, you want to be able to do it confidently knowing that it has been well engineered and fit for purpose. History in Australia tells us that not all switches are the same.
DC Switches are operated to add panels to an existing system, for maintenance purposes or the event of short circuiting.
One of the major challenges for disconnecting a DC load is the arc generated during the opening phase of the contact. Beside the enormous heat that is caused by the arc, the integrity of the contact surface is also suffering the longer the arc remains (without specific measures it can last up to 150 msec) which in the end could lead to a higher contact resistance respectively a loss in efficiency. The key criteria’s are contact opening time, isolating distance and arc time.
Recalls in Australia and Major Issues
In 2014 we saw voluntary recalls for solar DC isolator switches registered with the Australian Competition and Consumer Commission (ACCC).
Key Points:
- National Recall in Australia due to safety reasons affecting multiple manufacturers since 2011
- Main issue is overheating problems due to contact resistance
- Switches exposed to high ambient temperatures and direct sunlight
- Poor installation due style of enclosure and mounting methods
- Rebranding of rotary type switches that otherwise have been discontinued or banned from being sold
-
All of the rotary style DC isolators that were recalled experienced the same defect, localised heating, due to higher than desirable contact resistance occurring on one of the contact points. The failure mode was excessive heating at a contact when operation at normal current level.
The reason for this failure mode is to do with the design style of the switch using a spring loaded contact and a knife style terminal blade. As the rotary handle of the DC isolator is turned the Knife makes connection with the spring loaded contacts.

The rotary switch is fast acting spring loaded switch which allows the DC load to be made or broken fast with minimal arcing. The failure mode of this switch comes when the spring loaded contact force is not adequate, localised heating in most cases occurs which further reduces the contact force and worsens the situation.
The high contact resistance leads to localised heating at these points. As the metal parts within the isolator heat up they expand and distort very slightly. The spacer material that holds the contact may also soften and distort. This situation can lead to thermal runaway. As the contact points of the isolator expand / distort the contact resistance increases. This results in further localised heating, which in turn leads to a further increase in contact resistance. This process continues until the temperature is high enough to ignite surrounding combustible materials such as the plastic exterior case.
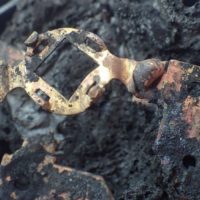
The example of the failed DC isolator shown in image above shows the molten copper and welded contact as a result from electrical arcing and extreme temperature (> 1085°C, the melting point of copper). The unpiloted ignition temperature of plastic is in the range of 400°C – 550°C.
To further exacerbate this failure, the solar panels circuits remain energised, assisting in the spread of fire. There is no protection element on the output of the DC solar panel array that can detect a fault inside the DC isolator and so the fault condition persists until a complete failure occurs.
Other investigations have found that the material selection (including the copper alloy contact material and the non-metallic material between these contacts) is not suitable for use in solar applications.
After the recalls the fundamental outcome was to consider the effect of temperature endurance of the switches.
Leveltec’s Partnership and Story
In 2014 Leveltec and MERZ Schaltgeräte GMBH + CO KG started a partnership for the distribution of its products and services through Australia and New Zealand . Merz a manufacturer of switchgear since 1946 has been a major supplier of AC and DC switchgear into the OEM market globally.
A leader in the market and pioneering the way for safe, reliable and robust switchgear, Merz is the undisputed exclusive supplier to worlds largest manufacturer of inverters. SMA has purchased switches for over 15 years has not had a single returned switch or reported failure.
Together attending various exhibitions and meetings with industry bodies over the course of 2014-2019 gave us a sound knowledge of the challenges in the market from the installer right to the regulator.
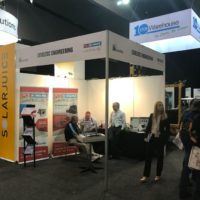
Knowing very well about the recalls in Australia and how Merz Switches differed from rotary style switches we set out to develop a solution for the market. From the beginning of the development we had the vision that the best way to guarantee the quality at the end user was to provide the switchgear in an enclosure as a complete engineered solution. This eliminated a number of challenges an installer needs to comply with and as we now know with hindsight, loose switches wasn’t a good thing.
Getting things right starts at the switch. One of the major challenges for disconnecting a DC load is the arc generated during the opening phase of the contact. Beside the enormous heat that is caused by the arc, the integrity of the contact surface is also suffering the longer the arc remains (without specific measures it can last up to 150 msec) which in the end could lead to a higher contact resistance respectively a loss in efficiency. The key criteria’s are contact opening time, isolating distance and arc time.
The contact material must be fit for purpose, the use of AgNi – Alloy offers a high safety against welding that is approximately 10 times higher than other material. It offers good resistance against the loss of contact materials and gives a low contact resistance for the lice cycle of the contact.
A switches long term reliability of 20 or more years needs to be considered and this is why Merz diligently considered the design with permanent and reliable contact pressure to overcome the optional problems cause by surface contamination resistance.
Breaking the contacts under load generates an arc which is ionizing the air inside the switch body. By generating a permanent and harmonized magnetic field inside the switch we are reducing the arc to a max. time of 3- 5 msec compared to 40 -150 msec without the inclusion of magnetic blow outs.
We searched wide for the best enclosures for the Australian market during international visit to Hanover fair only to find a suitable supplier in Australia of GRP enclosures. The GRP enclosure was selected as it had an IP66 rating, all external mounting screws, was impact resistant, non combustible and a 25 year design life for direct exposure to the sun.
Quickly in conjunction with Merz we prototyped at Leveltec the first MDC1 switches and exported them to Germany to be heat rise tested against the current Australia Standards. With exceptional results we continued supply of this style of switches to premium solar installer companies who accepted that for quality you must pay. The enclosure was rather large but did allow for easy termination.
Manufacturing lines began to establish for final assembly of all switchgear in Australia when amendments came through prohibiting the installation of loose switches in enclosures. The Switch enclosure must be an assembly from the manufacturer.
Pivoting quickly we worked in conjunction with Merz to address all the issues in the market and the new standards amendment to ensure we have a complying product. Many months of testing went into it to get it right.
We received overwhelming positive feedback regarding the product at the all energy exhibition when visited from groups like the clean energy council and utilities. Installers who in previous cases have been tasked with selection of switchgear didn’t have the appetite for a higher cost switch even when the quality was acknowledged. The common response was “well the $15 switch has a piece of paper too”
In 2021, a number of states have been contacted and advised that SAA Approvals pty ltd had cancelled 18 certifications for DC isolators. This means that any registrations associated with these DC isolators certifications were also cancelled as at 29 September 2021. Suppliers are not allowed to supply the affected DC isolators until they are re-certified and re-registered.
It appears that its possible some of the switches that gained compliance very quickly have now been added onto this list of DC isolators that cannot be sold. We hope that the regulators continue to uphold all manufactures to these high standards.
In the end, the market will determine how our industry moves forward in terms of how much we are willing to pay for compliance.
Head in the Right Direction
The result of the market changes in 2018 was the New MDC10, developed for Australia and manufactured in Germany!

Compliance:
- Tested and Certified to AS60947-3:2018
- AS/NZS IEC 60947.1:2015
- Utilisation category DC-PV2
- RCM & SAA Approval Number – SAA-193571-EA
- EESS Equipment Level 3 Number – E2020031687
- Complies with AS/NZ 5033:2014/Amdt 2:2018
Features:
- Enclosed and rated IP66NW
- +75/-25 Degrees Celsius souring air temperature
- Stainless steel lid Screws and all external mounting holes
- UV, Impact and Weather resistant for outdoor use
- 2 pole, 3 pole & 4 pole
- Use on systems in 1 and 2 MPPT configurations
- UV, Impact and Weather resistant for outdoor use
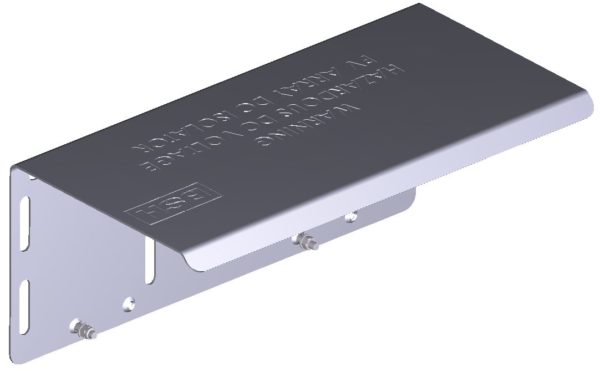
As the switchgear is always installed in conjunction with a bracket we also opted to manufacture a matching compliant bracket and conduit kit.
The sturdy bracket give multiple mounting options and the pre drilled mounting holes ensure when mounted it is fully complaint with correct clearance on each end and on top.
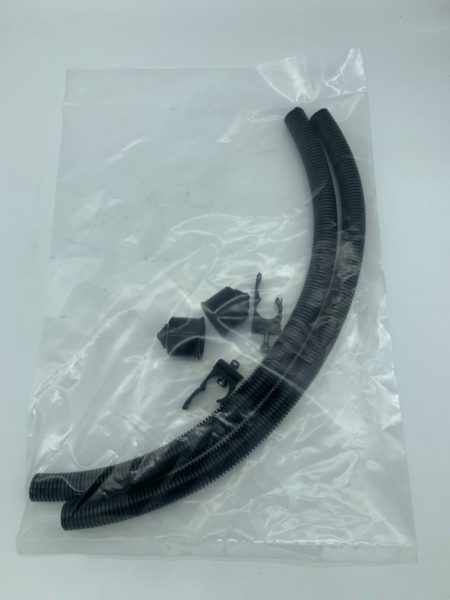
The conduit kit provides an added layer of mechanical protection and everything you need is in the bag. No need to carry multiple roles onto the roof, just grab a kit and go.
As the isolator is provided with matching glands to maintain the IP rating, these kits simple slide over the existing cables and gland. The conduit clamp is bolted or screwed to the rail to keep the cables up off the roof.
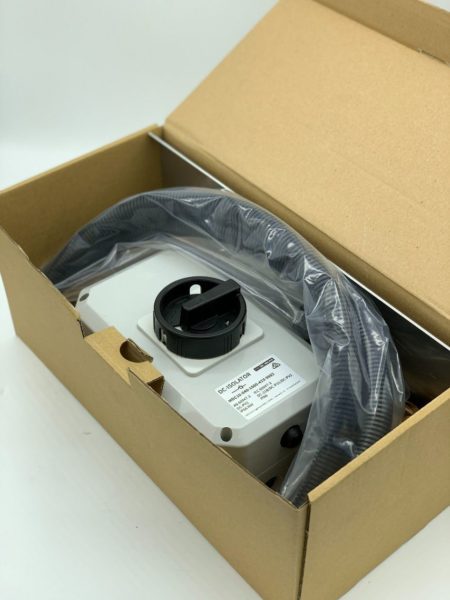
Switching to quality and maintaining compliance has never been easier for the solar industry.
By picking one of three isolator switches, adding the matching bracket and conduit kit you are well on your way to hassle free installs that are not only compliant but set and forget.
Related Topics – AC Isolators for Mirco Inverters
With increased requirements for isolator of micro inverters, Merz also offer the range of ML1 series isolators to compliment the MCDC10 Solar isolator Switchgear range.
- 690VAC Rated
- 1-3 Poles
- IP66 Enclosure
- ML1 series Switchgear